Trong sản xuất công nghiệp, máy đánh bóng từ tính là thiết bị xử lý bề mặt hiệu quả cao và thân thiện với môi trường, được sử dụng rộng rãi trong quá trình loại bỏ ba via, đánh bóng, làm sạch và các quy trình khác trong lĩnh vực chi tiết kim loại, dụng cụ chính xác, thiết bị y tế, đồ trang sức, v.v. Tuy nhiên, việc lựa chọn thiết bị không phù hợp có thể dẫn đến hiệu quả sản xuất thấp, lãng phí chi phí và thậm chí là các vấn đề về chất lượng sản phẩm. Do đó, thử nghiệm mẫu (tức là xác minh hiệu suất thiết bị thông qua các mẫu thực tế) là một bước quan trọng trước khi mua sắm chính thức. Phần sau đây phân tích tính cần thiết của nó từ nhiều khía cạnh.
- Kiểm tra tính tương thích của thiết bị và vật liệu
Nguyên lý cốt lõi của máy đánh bóng từ tính là truyền động kim thép không gỉ hoặc vật liệu mài mòn để tạo ra chuyển động tần số cao thông qua từ trường và cọ xát vào bề mặt phôi để đạt được hiệu quả đánh bóng. Tuy nhiên, các phôi làm từ các vật liệu khác nhau (như hợp kim nhôm, hợp kim titan, đồng, thép không gỉ, v.v.) có các yêu cầu rất khác nhau về các thông số như độ cứng, tần số chuyển động và cường độ từ trường của môi trường đánh bóng. Ví dụ:
Hợp kim nhôm tương đối mềm. Nếu sử dụng chất mài mòn có độ cứng cao hoặc từ trường tần số cao, bề mặt có thể bị trầy xước.
Hợp kim cứng (như cacbua vonfram) cần năng lượng đầu vào cao hơn để đạt được hiệu ứng mong muốn.
Thông qua thử nghiệm mẫu, có thể quan sát trực tiếp độ nhám bề mặt, độ chính xác về kích thước, độ bóng và các chỉ số khác của phôi sau khi đánh bóng để đảm bảo các thông số thiết bị phù hợp với tính chất vật liệu. Một nhà sản xuất phụ tùng ô tô đã từng mua thiết bị trực tiếp mà không qua kiểm tra, dẫn đến vỏ hợp kim nhôm sau khi đánh bóng bị trầy xước rất nhiều, gây thiệt hại hơn 500.000 nhân dân tệ.
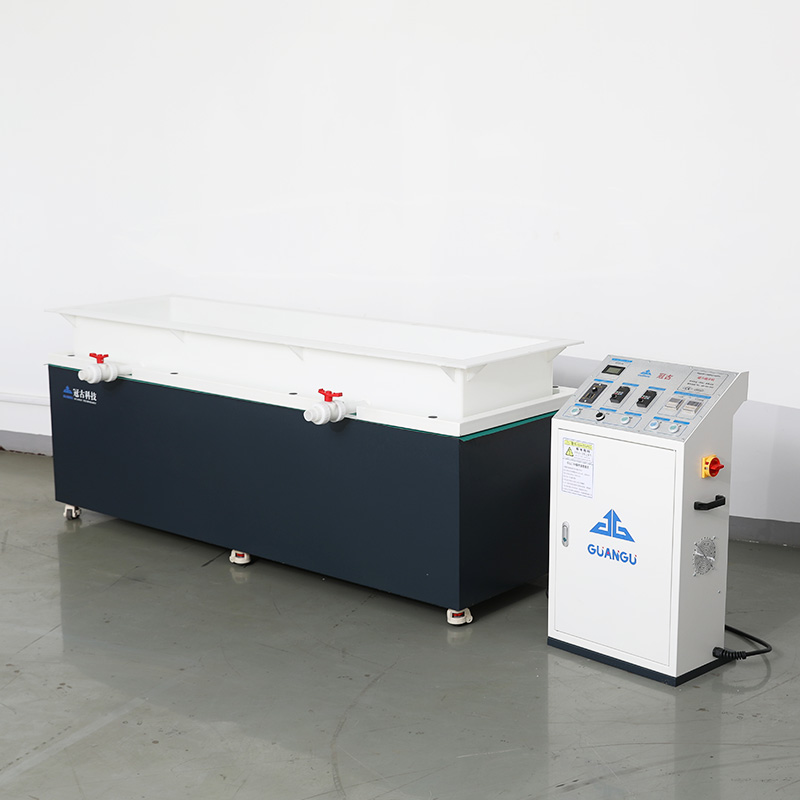
- Xác định các thông số quá trình tối ưu
Hiệu quả của máy đánh bóng từ tính bị ảnh hưởng bởi nhiều yếu tố như tần số từ trường, tỷ lệ mài mòn, thời gian xử lý và tốc độ điền đầy môi trường. Ví dụ:
Các bộ phận vi mô chính xác thường yêu cầu chế độ tần số cao, biên độ thấp để tránh biến dạng;
Các sản phẩm đúc lớn cần thời gian xử lý lâu hơn và vật liệu mài mòn có độ thô hơn.
Bằng cách thử nghiệm các kết hợp thông số khác nhau, có thể thiết lập được kế hoạch quy trình mục tiêu. Một công ty thiết bị y tế đã phát hiện thông qua thử nghiệm mẫu rằng bằng cách điều chỉnh thời gian xử lý từ 30 phút xuống 18 phút và thay thế chất mài mòn gốm, không chỉ hiệu quả tăng 40% mà còn tránh được hư hỏng lớp thụ động của dụng cụ phẫu thuật bằng thép không gỉ.
- Đánh giá hiệu quả xử lý của các cấu trúc phức tạp
Đối với các phôi có hình dạng hình học phức tạp như lỗ bên trong, ren, rãnh sâu, v.v., liệu lợi thế “không góc chết” của máy đánh bóng từ tính có thể được tận dụng đầy đủ hay không cần phải được xác minh thông qua thử nghiệm thực tế. Ví dụ:
Một công ty đồng hồ đã thử nghiệm và phát hiện ra rằng các lỗ trục bánh răng có đường kính nhỏ hơn 0,5 mm vẫn còn các gờ còn sót lại theo thông số tiêu chuẩn và cần phải có vật liệu mài mòn có hình dạng đặc biệt tùy chỉnh;
Một nhà cung cấp phụ tùng hàng không vũ trụ đã so sánh phôi trước và sau thử nghiệm quét 3D và xác nhận rằng độ nhám của thành bên trong kênh làm mát có tỷ lệ chiều sâu/chiều rộng là 5:1 đã giảm từ Ra3,2μm xuống Ra0,4μm.
Loại kết quả thử nghiệm dựa trên dữ liệu này là cơ sở đưa ra quyết định trực tiếp nhất cho việc lựa chọn thiết bị.
- Tránh rủi ro đầu tư
Giá của một máy đánh bóng từ tính cỡ trung bình thường nằm trong khoảng từ 100.000 đến 500.000 nhân dân tệ, nếu không đáp ứng được nhu cầu sau khi mua sẽ dẫn đến lãng phí tài nguyên nghiêm trọng. Một nhà máy gia công phần cứng đã từng mua thiết bị mà không thử nghiệm, sau đó phát hiện ra rằng cường độ từ trường của thiết bị không đủ để xử lý các tấm thép dày hơn 20mm. Cuối cùng, tỷ lệ nhàn rỗi của thiết bị lên tới 70%. Ngược lại, thử nghiệm mẫu có thể phát hiện trước các vấn đề tiềm ẩn, chẳng hạn như:
Tải trọng tối đa của thiết bị có phù hợp với quy mô sản xuất hay không;
Mức tiêu thụ năng lượng có đáp ứng tiêu chuẩn cung cấp điện của nhà máy hay không;
Tiếng ồn và độ rung có vượt quá yêu cầu của môi trường xưởng không.
- Tối ưu hóa tổng chi phí
Trong quá trình thử nghiệm, chi phí xử lý của một sản phẩm riêng lẻ (bao gồm hao hụt vật liệu mài mòn, mức tiêu thụ điện, chi phí nhân công, v.v.) có thể được định lượng và đánh giá. Một công ty chế biến đồ trang sức đã phát hiện thông qua thử nghiệm so sánh:
Đánh bóng trống truyền thống: chi phí cho mỗi sản phẩm là 1,2 nhân dân tệ, tỷ lệ đạt yêu cầu là 85%;
Đánh bóng từ tính: Chi phí cho mỗi sản phẩm là 0,8 nhân dân tệ, tỷ lệ đạt yêu cầu tăng lên 98%.
Ngoài ra, việc thử nghiệm có thể giúp các công ty lựa chọn loại vật liệu mài mòn tiết kiệm chi phí nhất. Ví dụ, một công ty ban đầu dự định mua kim thép không gỉ nhập khẩu (đơn giá 120 nhân dân tệ/kg), nhưng sau khi thử nghiệm đã chuyển sang vật liệu mài mòn gốm tổng hợp trong nước (đơn giá 60 nhân dân tệ/kg), đạt được hiệu quả tương tự trong khi tiết kiệm được 150.000 nhân dân tệ chi phí vật tư tiêu hao hàng năm.
- Kiểm tra độ ổn định của thiết bị và các yêu cầu bảo trì
Kiểm tra hoạt động liên tục đánh giá tính ổn định lâu dài của thiết bị. Một trường hợp cho thấy sau khi một loại thiết bị nhất định hoạt động liên tục trong 8 giờ, nhiệt độ của máy phát từ trường tăng lên 85°C, làm giảm 12% hiệu suất đánh bóng. Những vấn đề như vậy rất khó phát hiện trong một cuộc trình diễn ngắn hạn, nhưng có thể phát hiện được thông qua thử nghiệm mẫu trong 72 giờ.
- Kiểm tra tính khả thi của các yêu cầu tùy chỉnh
Đối với các ngành công nghiệp chuyên biệt, chẳng hạn như đánh bóng đế bán dẫn, có thể cần đến máy tạo từ trường tùy chỉnh hoặc phát triển các đồ gá chuyên dụng. Một công ty bán dẫn đã xác nhận thông qua thử nghiệm mẫu rằng nhà cung cấp của họ có thể phát triển giải pháp đánh bóng không tiếp xúc cho bộ phận mang wafer silicon đường kính 300mm để tránh nhiễm bẩn hạt do tiếp xúc cơ học thông thường.
- Đánh giá năng lực kỹ thuật của nhà cung cấp
Quá trình thử nghiệm về cơ bản là phép thử độ chính xác về năng lực kỹ thuật của nhà cung cấp. Các nhà cung cấp chất lượng cao sẽ cung cấp:
Nhiều giải pháp thay thế;
Theo dõi và báo cáo dữ liệu theo thời gian thực;
Đề xuất tối ưu hóa tham số quy trình.
Một nhà sản xuất thiết bị của Đức đã từng tiến hành 20 bộ thử nghiệm so sánh cho khách hàng trong nước và cuối cùng đã tăng tỷ lệ đánh bóng đạt yêu cầu từ 89% lên 99,5%. Khả năng dịch vụ chuyên sâu này chỉ có thể được chứng minh thông qua thử nghiệm thực tế.
kết luận
Thử nghiệm mẫu là cầu nối quan trọng giữa hiệu suất lý thuyết của thiết bị với nhu cầu sản xuất thực tế. Nó không chỉ có thể tránh được rủi ro trong mua sắm mà còn thiết lập hệ thống quy trình chuẩn hóa cho doanh nghiệp thông qua việc tích lũy dữ liệu khoa học. Các công ty được khuyến nghị:
Cung cấp các hiện vật tiêu biểu mang tính đại diện;
Chỉ định các tiêu chí chấp nhận về mặt định lượng (ví dụ: độ nhám, độ bóng, phạm vi dung sai);
Các nhà cung cấp phải cung cấp báo cáo thử nghiệm đầy đủ (bao gồm hồ sơ video, dữ liệu thử nghiệm và khuyến nghị về thông số).
Chỉ bằng cách vượt qua các bài kiểm tra kiểu dáng nghiêm ngặt, chúng tôi mới có thể đảm bảo rằng máy đánh bóng từ tính chuyển từ “có thể sử dụng” sang “dễ sử dụng” và thực sự trở thành một công cụ sản xuất để nâng cao khả năng cạnh tranh cốt lõi.